For those who crave individuality and love to wear their unique style, the ability to print t-shirts at home is a game-changer. No longer do you have to settle for mass-produced designs when you can bring your creative vision to life.
In this blog post, we’ll dive into the world of DIY t-shirt printing, sharing tips, tricks, and step-by-step instructions to help you master the art of crafting custom tees right from the convenience of your own home.
what do i need to print t shirts at home: Equipment and Materials
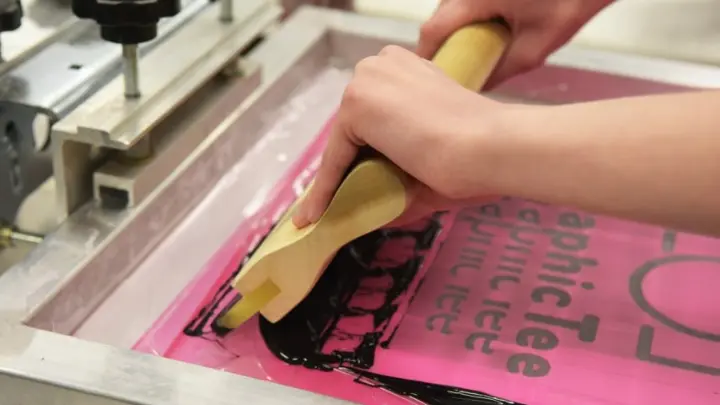
When it comes to printing your own T-shirt at home, having the right materials on hand is crucial for achieving a professional and long-lasting result. This section outlines the essential materials you’ll need to embark on your T-shirt printing journey from the comfort of your home
T-shirt or Selected Fabric
Begin your custom print project by choosing a suitable base material. The fabric, preferably a t-shirt or any textile of your choice, will serve as the canvas for your artwork. Consider the color and texture of the fabric, as these factors will influence the final appearance of your printed design.
Plastic Wrap
Plastic wrap plays a crucial role in the image transfer process. It acts as a protective barrier, ensuring that the ink from your graphic does not directly contact the iron and prevents the image from smudging. Make sure to have enough plastic wrap to completely cover your print.
Parchment Paper
Parchment paper is a must-have in this process. It’s used as a protective layer between the iron and the plastic-wrapped print. This barrier is essential to prevent the print from sticking to the iron, ensuring a smooth and clean transfer of your graphic onto the fabric.
Graphic Print
Select and print the graphic that you wish to transfer onto your fabric. The quality and size of the print are significant; a clear, high-resolution image will ensure a detailed and vibrant transfer. An 11×17 inch print is recommended if you’re aiming for a large, impactful design on your fabric.
Scissors
Scissors are a simple yet essential tool in your materials list. You’ll need a sharp pair to precisely cut the print to your desired shape and size. Also, scissors will be necessary to cut the plastic wrap accurately, ensuring it fits perfectly over your graphic print.
Iron
An iron is the primary tool for the transfer process. Before starting, ensure that the iron is set to a no-steam setting and that all water is removed to prevent moisture from affecting the transfer. The heat from the iron will effectively transfer the ink from the paper to your fabric, embedding your chosen graphic into the material.
Ironing Board or Heat-Resistant Surface
Lastly, prepare an appropriate surface for the ironing process. An ironing board is ideal due to its padded surface and heat-resistant cover. However, any flat, stable, and heat-resistant surface will suffice. Ensure that the area is spacious enough to accommodate your fabric and allows for easy maneuvering of the iron during the transfer process.
A Guide to Choosing the Right Material for Custom T-Shirts
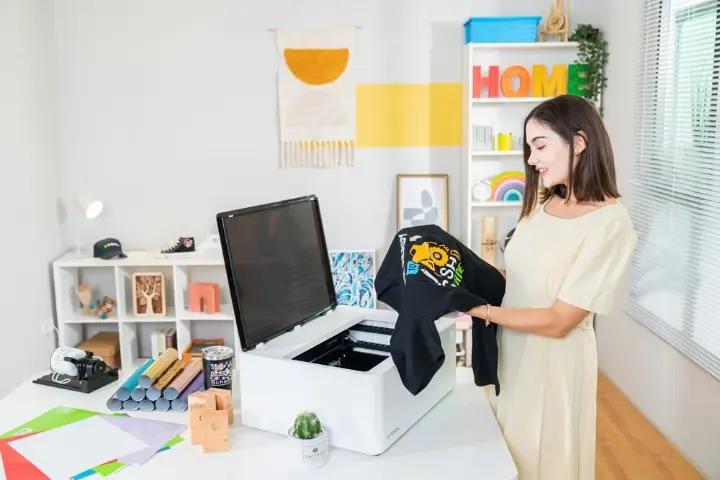
Selecting the ideal material is a pivotal step in custom t-shirt creation, influencing comfort, durability, and style. This concise guide offers essential insights to help you navigate the choices, ensuring your custom t-shirts meet your exact needs and expectations, whether for business, personal use, or retail.
Understand the Different Types of Fabrics
Different fabrics offer varying qualities, making them suitable for specific types of t-shirts and printing methods. Cotton is revered for its softness and breathability, making it a comfortable choice for everyday wear.
Polyester stands out for its strength, durability, and moisture-wicking properties, ideal for sportswear and active apparel. Blends, especially those of cotton and polyester, offer a balance, inheriting the positive qualities of both materials, and are versatile across various printing techniques.
Consider the Printing Technique
The choice of fabric should be influenced by the printing technique to ensure optimal results. Screen printing, favored for its vibrancy and durability, pairs well with most fabrics, particularly cotton.
DTG printing is best suited for high-thread-count, tight-knit fabrics like 100% cotton, delivering precision and color depth. Sublimation printing, known for its fade-resistant and detailed prints, requires fabrics with high polyester content to ensure proper ink adhesion and longevity.
Factor in the Shirt’s Purpose
The intended use of the t-shirt should guide the fabric choice. For casual, everyday wear, prioritize comfort by choosing soft fabrics like cotton or comfortable blends. For sportswear, opt for polyester or blends that offer moisture-wicking to keep the wearer dry and comfortable. For promotional wear meant for short-term use but requiring durability, blends or pure polyester can be both cost-effective and resilient.
Evaluate Fabric Quality
Quality is key to the longevity and appearance of the t-shirt. A higher thread count generally means a softer and more robust fabric, enhancing the print’s look and the shirt’s feel. Fabric weight is another consideration; heavier fabrics tend to be sturdier but may not be as comfortable in warmer climates. Also, the fabric’s texture can affect the print quality, so choose a texture that complements your design and printing technique.
Consider the Fabric Color
The color of the fabric can significantly impact the appearance of your print. Light-colored fabrics typically make colors pop and are versatile for various designs. In contrast, dark fabrics provide a striking backdrop for bold, light-colored designs but may require a white underbase for certain printing techniques to ensure color accuracy and vibrancy.
A Step-by-Step Guide to Print T-shirt at Home
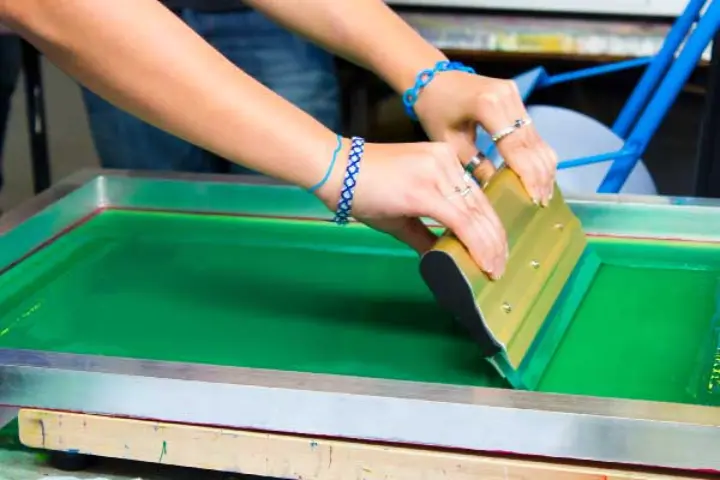
The journey from a design concept to a beautifully printed T-shirt involves meticulous preparation and attention to detail. Below, each step of this creative process is broken down to ensure a flawless transfer of your unique print onto a T-shirt.
Prepare Your Print and Iron
Begin by carefully trimming around your print. Leave a slight margin to ensure a clean edge and to avoid any unwanted tearing or fraying during the transfer process. While preparing your print, plug in your iron and set it to a no-steam setting.
Allow it to heat up thoroughly. Meanwhile, lay out your T-shirt and iron it flat, especially focusing on the area where you intend to place your print. This step is crucial to eliminate any wrinkles or moisture, as a smooth, dry surface is key for a successful transfer.
Wrap the Print with Precision
Place your print on a sheet of plastic wrap, ensuring that the plastic extends slightly beyond the edges of the print. This extra plastic wrap will protect the print and aid in a clean transfer. Carefully cover the print with another layer of plastic wrap, creating a sandwich-like structure. This protects your print from direct heat during the ironing process and ensures the ink or design doesn’t smear. Trim the excess plastic but leave about half an inch around the print, folding it neatly behind. This step is pivotal as it prevents any ink from bleeding out during the transfer and ensures a crisp edge to your design.
Set Up the Transfer
Carefully position the wrapped print on the T-shirt, placing it exactly where you want your design to appear. Once positioned, cover the print with a sheet of parchment paper. The parchment paper acts as a protective barrier, preventing the plastic wrap from melting onto the iron or causing any damage to the print itself. It also distributes the heat evenly across the print, ensuring every part of the design receives the necessary temperature to adhere properly.
Iron with Care and Inspect
Press the iron firmly over the parchment paper. Apply moderate, even pressure and focus on all areas, especially the edges and corners of the print. These areas are most prone to lifting or not transferring properly, so they may require additional attention. After ironing, gently peel back a corner of the parchment paper to inspect the transfer.
Look for any signs of lifting, bubbling, or incomplete transfer. If you spot any issues, simply lay the parchment paper back down and re-iron those specific areas, ensuring the entire design adheres smoothly to the fabric.
Finalize the Transfer
Once you’re satisfied with the transfer, allow the print to cool down. This cooling period is crucial as it lets the plastic wrap solidify and ensures the print sticks to the fabric. After cooling, carefully remove the parchment paper. If done correctly, your custom graphic should now be seamlessly integrated onto the T-shirt, boasting vibrant colors and sharp edges. Admire your work, and you’re ready to sport or gift your personalized T-shirt.
By attentively following these five steps, you can transform any plain T-shirt into a masterpiece of your own creation. Each phase, from preparation to finalization, is crucial in ensuring the longevity and quality of your print.
Setting Up Your Printing Workspace

Creating an efficient and well-organized workspace is crucial for streamlining the t-shirt printing process at home. Start by designating a specific area in your home that is well-ventilated and free from dust and debris, as these can affect the quality of your prints.
Ensure that this space is equipped with a flat, stable surface to place your printing equipment and materials. Adequate lighting is also essential, as it helps in accurately checking the alignment and quality of the prints.
Invest in proper storage solutions for your inks, screens, and other supplies to keep your workspace tidy and to prolong the life of your materials. Keep your most-used tools within arm’s reach to improve workflow efficiency. If you’re using equipment like heat presses or screen-printing machines, make sure there’s enough space to operate them safely.
Lastly, consider the cleanliness of the area. Regularly cleaning your workspace can prevent accidental stains or damage to your t-shirts and equipment. Setting up your workspace thoughtfully will not only make the printing process smoother but also more enjoyable.
Troubleshooting Common Printing Issues
Encountering printer problems can be highly frustrating. This section offers a concise guide to quickly identify and solve the most frequent printing issues. From paper jams to poor print quality, you’ll find practical troubleshooting tips to get your printer back to working order efficiently, ensuring minimal disruption whether at home or in the office.
Ink Not Adhering to the Fabric
One of the most common issues is the ink not sticking properly to the fabric. This can be due to a variety of factors, such as incorrect curing time or temperature, or using ink that’s not compatible with your fabric. To solve this, ensure that you’re using the right type of ink for your fabric and that you’re following the manufacturer’s guidelines for curing.
Uneven Ink Distribution
If you notice that the ink is not evenly distributed across your design, it could be due to uneven pressure during the printing process or a clogged screen. Make sure that your screen is clean and free of any blockages, and practice applying consistent pressure while printing.
Color Fading After Washing
If the vibrancy of your T-shirt designs fades after washing, it’s likely an issue with the ink curing process. Ensure that you’re curing the ink at the right temperature and for the correct amount of time. Using a heat press can provide more consistent results than air-drying.
Image Clarity
Blurred or distorted images can result from a screen that’s not properly tensioned or from using an incorrect mesh count for your screen. Ensure that your screen is tightly secured and that you’re using the right mesh count for the level of detail in your design.
Fabric Damage
Excessive heat or pressure can damage fabrics, especially delicate ones. Always check the fabric’s heat tolerance and adjust your printing process accordingly. It’s also a good idea to do a test print on a similar fabric to ensure that your settings are correct.
Remember, practice makes perfect. Don’t get discouraged by these common issues. With patience and perseverance, you’ll be able to troubleshoot your way to stunning, professional-quality T-shirts right from your home. Keep experimenting with different techniques and settings, and soon you’ll find the perfect combination that works for your specific needs.
Marketing Your T-Shirts: Strategies for Home-Based Businesses
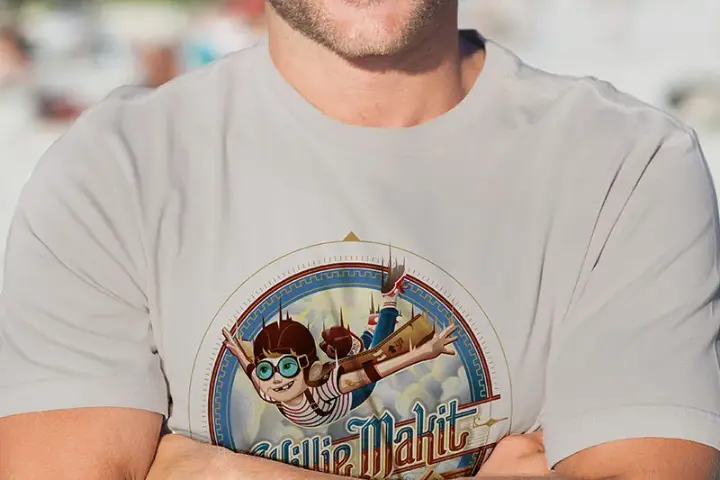
Elevate your home-based t-shirt business with a dynamic marketing strategy. Capitalize on social media platforms like Instagram and Facebook to showcase your designs and engage with your audience. A professional, SEO-optimized website acts as your digital storefront, complete with an intuitive online store.
Supplement your online presence with targeted email marketing, offering personalized content and exclusive deals to keep your audience engaged. Don’t underestimate the value of physical presence; participating in local events can significantly bolster customer relationships. Incentivize loyalty and attract new customers with promotions, discounts, and a referral program.
Consider investing in targeted paid advertising on platforms like Google and Facebook to expand your reach. A successful marketing approach combines digital engagement, community interaction, and strategic promotions, transforming your home-based venture into a thriving brand.
Conclusion
Venturing into home t-shirt printing is a fusion of creativity and skill. With essential tools and a flair for design, you’re ready to transform simple tees into expressions of your unique style.
This journey is more than a hobby—it’s a platform for personal expression and potential entrepreneurship. Dive into the world of fabric and ink, and let your designs narrate your creative tale. Welcome to the dynamic realm of home t-shirt printing!