What do i need to make t shirts? Are you ready to dive into the world of custom iron-on t-shirts? Whether you’re crafting shirts for a special event or simply expressing your personal style, creating your own custom apparel can be both fun and rewarding.
In this comprehensive guide, we’ll walk you through the essential steps and tools you’ll need to make your own unique t-shirts from start to finish.
What Do I Need to Make T Shirts: Essential Equipment
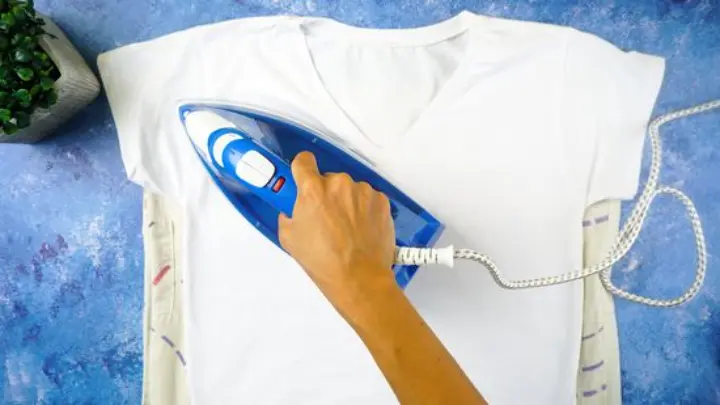
To embark on your t-shirt making journey, you’ll need a set of essential tools and equipment. Here’s a breakdown of what you’ll require:
Heat Press Machine
A heat press machine is a fundamental tool for transferring your designs onto t-shirts. It applies heat and pressure to imprint graphics onto fabric efficiently. When choosing a heat press machine, consider factors such as size, temperature control, and pressure adjustment to ensure it meets your specific needs.
Screen Printing Kit
Screen printing offers a versatile and professional-quality method for printing designs on t-shirts. A screen printing kit typically includes screens, squeegees, inks, and emulsions. Mastering the screen printing technique may require some practice, but it offers excellent results once you get the hang of it.
Vinyl Cutter and Heat Transfer Vinyl
For those who prefer a simpler and more precise method, a vinyl cutter paired with heat transfer vinyl provides an excellent alternative. This method involves cutting designs out of vinyl sheets and then using a heat press to transfer them onto t-shirts. It’s ideal for intricate designs and small production runs.
Sublimation Printer and Ink
Sublimation printing involves transferring designs from special sublimation ink onto t-shirts using heat and pressure. To get started, you’ll need a sublimation printer capable of printing onto transfer paper and sublimation ink. This method is popular for its vibrant and durable results, especially on polyester fabrics.
Blank T-Shirts
Blank t-shirts serve as the foundational canvas upon which your creative visions materialize. Opting for t-shirts crafted from premium-quality fabrics, such as cotton or cotton-polyester blends, in an array of sizes and hues ensures versatility in accommodating diverse design preferences.
Printing Supplies
Tailoring your choice of printing supplies to align with your preferred technique is pivotal. Whether it be screen printing ink, heat transfer vinyl, sublimation paper, or sublimation ink, ensuring an ample supply of these materials is essential for sustaining seamless production operations.
Design Software
Harnessing the power of design software is indispensable for bringing your t-shirt concepts to fruition. Whether you possess proficiency in graphic design software such as Adobe Illustrator or gravitate towards user-friendly alternatives like Canva, selecting a tool that harmonizes with your skill level and design aspirations is imperative.
Protective Gear
Prioritizing safety amidst the t-shirt-making process is non-negotiable. Equipping yourself with an array of protective gear, including heat-resistant gloves, aprons, goggles, and respiratory masks, safeguards against potential hazards inherent in working with heat press machines, screen printing chemicals, and vinyl cutting equipment.
What Do I Need to Make T-Shirts: A Guide to Choosing the Right Ones
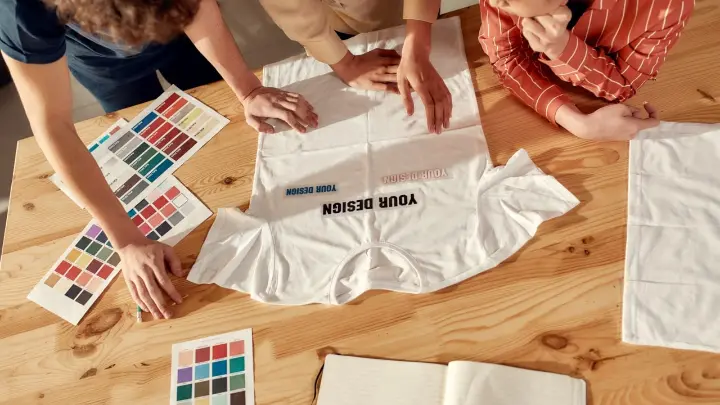
Choosing the right materials is crucial when making t-shirts, as it directly impacts the quality and durability of the final product. Here are some key factors to consider when selecting materials for your t-shirt-making project:
Fabric Quality
The fabric you choose will determine the comfort and longevity of your t-shirt. Opt for high-quality materials like 100% cotton or a cotton-polyester blend for a soft feel and good durability. Consider the weight of the fabric as well; lighter fabrics are ideal for warm weather, while heavier fabrics provide more warmth and structure.
Color and Print
Decide on the color and print of the t-shirt fabric based on your design preferences and intended use. Solid colors provide a clean canvas for bold designs or graphics, while patterned or textured fabrics can add visual interest to your t-shirts. Keep in mind that lighter colors may require additional layers of ink or material for opaque coverage, especially when using iron-on transfers.
Ease of Printing and Decoration
If you plan to customize your t-shirts with prints, embroidery, or appliques, consider the ease of working with the fabric. Smooth, flat surfaces are ideal for printing and heat transfers, while textured or stretchy fabrics may pose challenges. Choose a fabric that accommodates your chosen decoration methods and provides a stable base for your designs.
Durability and Care
Consider the durability and care requirements of the fabric, especially if the t-shirts will be subjected to frequent wear and washing. Look for fabrics that are colorfast and resistant to fading, shrinking, and pilling. Check the care instructions to ensure that the fabric is easy to clean and maintain, whether through machine washing or dry cleaning.
Environmental and Ethical Considerations
In addition to quality and performance, you may also want to consider the environmental and ethical aspects of the materials you choose. Look for fabrics made from sustainable or organic fibers, as well as those produced using eco-friendly manufacturing processes. Consider the ethical practices of the manufacturers and suppliers to ensure that your materials are sourced responsibly and ethically.
By carefully considering these factors, you can choose materials that not only meet your design and performance needs but also align with your values and priorities. Whether you’re making t-shirts for personal use, selling them commercially, or gifting them to others, selecting the right materials is essential for creating high-quality, stylish, and sustainable garments.
The T-Shirt Making Process: Step by Step
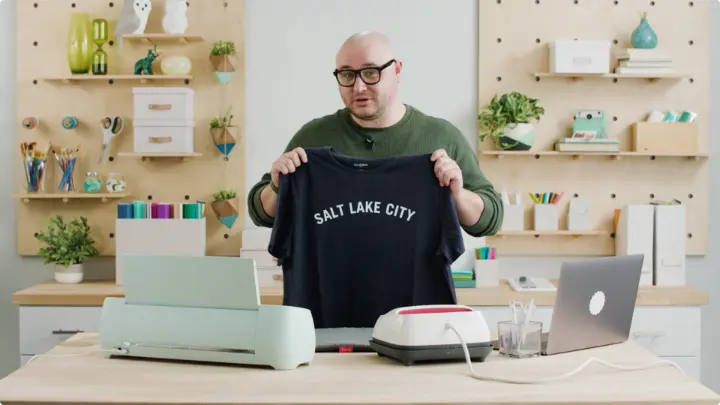
Design Preparation: From Digital Sketches to Printable Formats
Once you have finalized your designs, it’s time to prepare them for printing. This involves digitizing hand-drawn sketches or creating digital artwork using graphic design software. Ensure your designs are properly sized and formatted for printing, taking into account factors such as placement and color separation for multi-color prints.
Cutting and Weeding: Precision in Every Detail
If you’re using heat transfer vinyl, the next step is to cut out your designs using a cutting plotter. After cutting, you’ll need to weed away the excess vinyl from around your designs, leaving only the desired elements intact. This process requires patience and attention to detail to ensure clean, accurate cuts and smooth weeding.
Heat Press Application: Bringing Your Design to Life
With your designs prepared and cut, it’s time to transfer them onto your t-shirts using a heat press machine. Follow the manufacturer’s instructions for temperature, pressure, and pressing time to ensure proper adhesion and durability. Take care to position your designs accurately on the t-shirts for professional-looking results.
Screen Printing: The Art of Layering Colors
For those opting for screen printing, the process involves creating screens for each color in your design and applying them sequentially to build up the final image. This technique requires precision and attention to detail to ensure proper registration and color alignment. With practice and experience, you can master the art of screen printing and produce stunning, multi-color designs.
What Do I Need to Make T-Shirts: Troubleshooting Common Issues
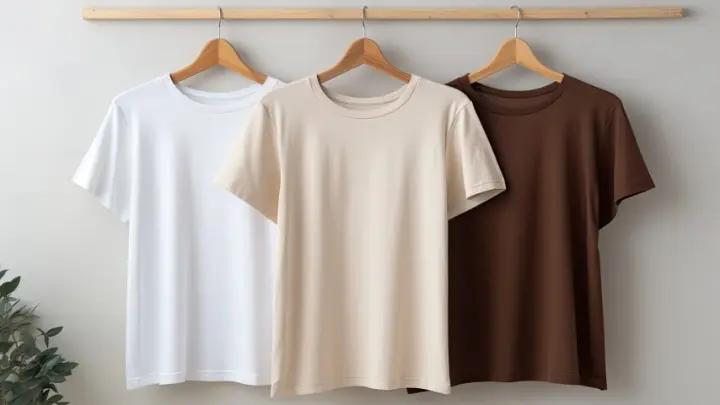
Ensuring Proper Heat Press Temperature and Pressure
Inconsistent temperature and pressure can result in subpar adhesion and durability of your prints. Invest in a quality heat press machine and regularly calibrate it to ensure accurate temperature and pressure settings. Conduct test prints and adjustments as needed to achieve optimal results.
Addressing Vinyl Application Challenges
Vinyl application can sometimes be tricky, especially when dealing with intricate designs or fine details. Ensure your cutting plotter is properly calibrated and your blades are sharp to achieve clean, precise cuts. Additionally, take care when weeding to avoid damaging delicate elements of your designs.
Troubleshooting Screen Printing Mishaps
Screen printing can present its own set of challenges, from ink bleeding to registration errors. Troubleshoot these issues by ensuring proper screen tension, using the correct mesh count for your designs, and fine-tuning your printing technique. With patience and persistence, you can overcome these obstacles and achieve professional-quality screen prints.
FAQs
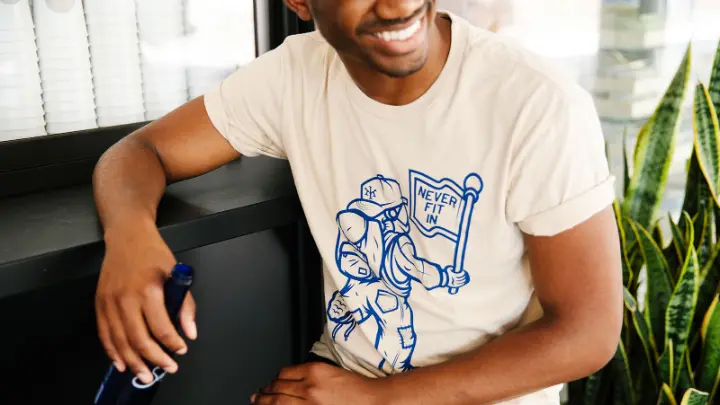
Do I need artistic skills to design t-shirts?
While artistic skills certainly help in creating visually appealing designs, they are not necessarily required to make t-shirts. Many beginners start with simple designs or text-based graphics that can be easily created using graphic design software or purchased from online marketplaces. With practice and experimentation, you can develop your design skills and create unique t-shirts that reflect your style and personality.
How do I ensure my t-shirt designs are durable and long-lasting?
Ensuring the durability of your t-shirt designs involves using high-quality materials and proper application techniques. Invest in premium heat transfer vinyl and screen printing ink that are specifically formulated for use on textiles, as these materials offer superior adhesion and wash-fastness. Additionally, follow manufacturer guidelines for temperature, pressure, and curing times to ensure your designs withstand repeated washing and wear.
Can I start a t-shirt business from home?
Yes, starting a t-shirt business from home is entirely possible with the right equipment, materials, and dedication. Many entrepreneurs successfully launch small-scale t-shirt businesses from their homes, selling custom designs online or at local markets and events.
However, it’s essential to research local regulations, obtain any necessary permits or licenses, and invest in marketing efforts to attract customers to your business. With creativity and entrepreneurial spirit, you can turn your passion for t-shirt making into a profitable venture from the comfort of your own home.
Can I make t-shirts without a heat press machine?
While a heat press machine is the preferred method for applying designs to t-shirts, it is possible to achieve similar results using alternative methods such as an iron or a handheld heat press. However, these methods may not offer the same level of precision, consistency, and durability as a dedicated heat press machine. Additionally, using an iron requires careful attention to temperature and pressure to ensure proper adhesion and longevity of your designs.
What’s the difference between heat transfer vinyl and screen printing?
Heat transfer vinyl involves cutting designs from vinyl sheets and applying them to t-shirts using a heat press machine, resulting in a smooth, raised finish. On the other hand, screen printing involves transferring ink through a mesh screen onto the fabric, allowing for vibrant, long-lasting prints with excellent color saturation.
While both methods have their advantages, heat transfer vinyl is better suited for small-scale or custom orders, while screen printing is more cost-effective for larger production runs.
Conclusion
Making custom t-shirts with iron-on material is a creative and enjoyable process that allows you to express your individuality and style. With the right tools and materials, along with a bit of creativity, you can design and create personalized apparel for any occasion.
So, gather your supplies, unleash your creativity, and start making your own custom t-shirts today!